See Texas A&M University materials science and engineering senior capstone projects from fall 2020 to spring 2021.
Projects
Project 1
Corrosion and reliability assessment for metallic fixtures in galvanized process applications
Duration: Two semestersTeam members: Carrie Jones (lead), Amee Rivers, Garrett Smola , Julia Stephenson, Samuel Bowen
Synopsis: This scope of work describes a corrosion assessment and reliability study of the metallic fixtures used during preconditioning and hot galvanizing process. The capstone design project includes the surface evolution and damage accumulation of the metallic asset following the acid-dry-hot-dip cycling process. The study comprises steel fixture samples submerged in an acid bath following a dry condition and then immerse in molten zinc with different load conditions. The metallic asset will be studied and characterized in terms of the characterization analysis; this same methodology will be used for different materials. The corrosion and performance assessment will be proposed based on an integrated study of damage testing of different metallic samples subjected to temperature, corrosive, loading and dry-wet cycling conditions by simulating the preconditioning processes before and during the hot dipping galvanized process.
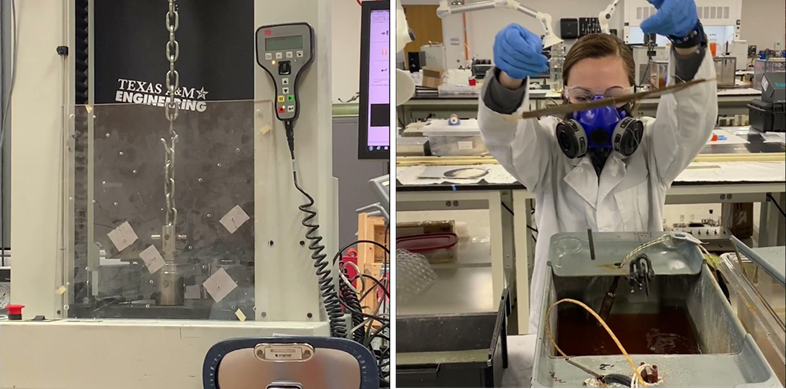
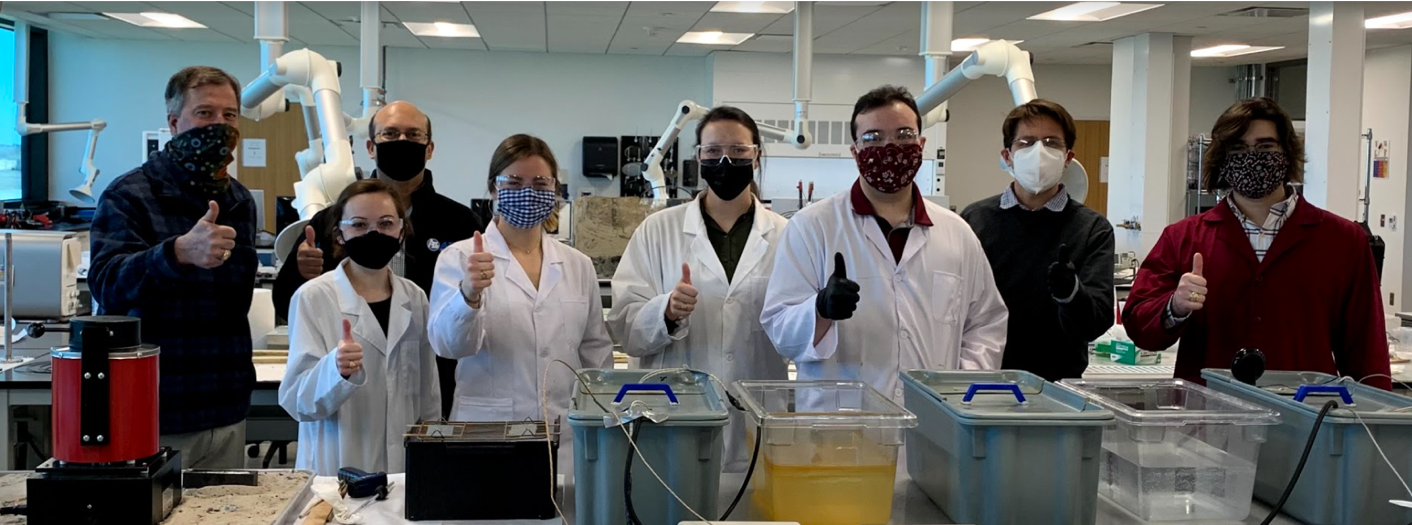
Project 2
Root cause failure assessment of Ni-Al-Bronze bolts in seawater
Duration: Two semestersTeam members: Micaela Torres (lead), Bianca Avila, Brian Gilbert, Drew Stessel , Jeremy Grayless
Synopsis: 可怜的生产规范,不正确的材料selection, or inadequate quality assurance or quality control during production of parts can not only lead to material failure, but also loss of primary containment (LOPC), oftentimes resulting in release of hydrocarbons to the environment and operational limits. In the first Semester, the students will carry out failure Analysis of as-failed Ni-Al-Br bolts in a marine offshore environment leading to loss of primary containment. This will involve detailed characterization of fracture surface, including evaluation of fracture mode, microstructural, and chemical analysis, and identification of failure mechanism. In the second semester, the students will carry out gasket and bolt immersion testing in simulated environment; perform chemical analysis of bi-products in the solution; and characterize bolt surface condition including chemical analysis after exposure to assess effect of bi-products on bolt and root cause of failure as applicable.
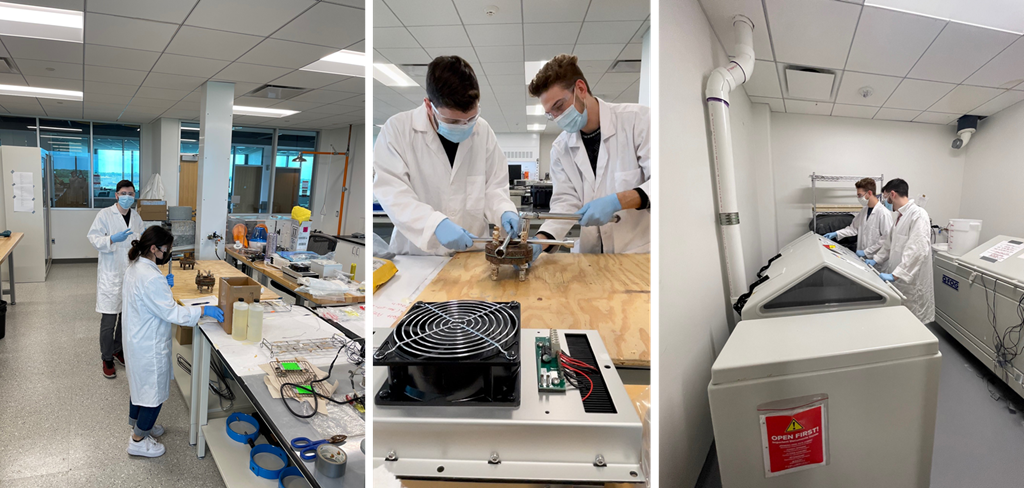
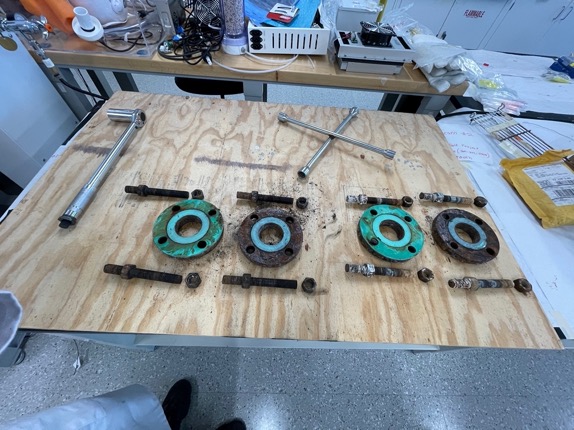
Project 3
Mechanical Testing of Fiberglass Reinforced Polymeric handrails
Duration:One semester
Team Members:Nathaniel Lies (lead), DavidSetien, Ines Figueroa-Casas, Julia Taylor, Maurilio Yanez
Synopsis: FRP structural and pressure containing materials are commonly used materials solutions in lieu of metallic materials to reduce deterioration and prevent failures due to corrosion and help the environment by reducing energy during their processing and lower gas emissions to help people and the environment, however, their mechanical, chemical, and physical property limits need to be understood in more depth for specific applications where metallic components are a standard solution. For instance, understanding the operating limits of FRP when exposed to pool fire is key when considering substitution of metallic materials. In this project, the students will design and conduct mechanical testing under specific conditions, pool fire experiments, and characterize materials pre and post pool fire testing to evaluate their integrity.
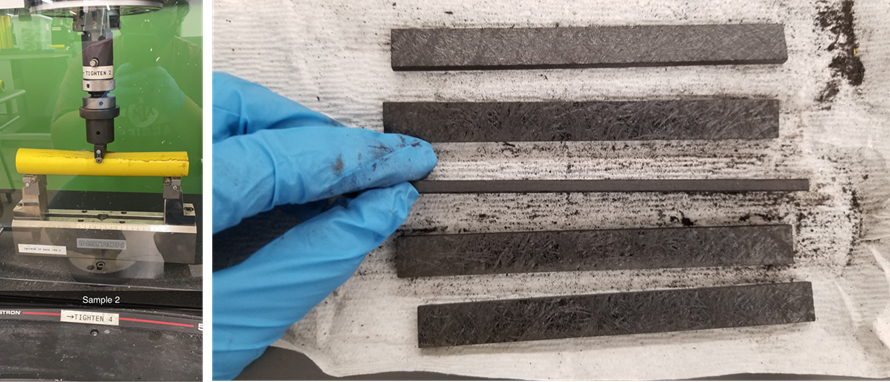
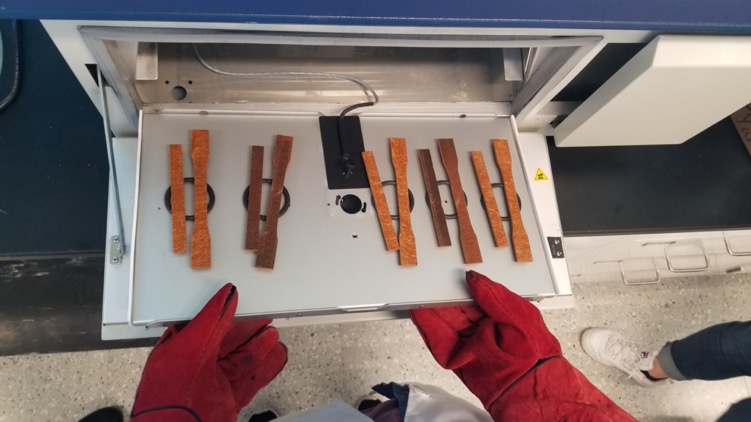
Project 4
Correlation of density to additively manufactured metallic part performance
Duration:One semester
Team members:Nathaniel Lies (lead), DavidSetien, Ines Figueroa-Casas, Julia Taylor, Maurilio Yanez
Synopsis:Additive manufacturing techniques often use theoretical density as a benchmark for process development, qualification, and quality assessment. Density is also used as a quick and convenient non-destructive measure of process performance of co-printed parts. However, this measurement does not necessarily relate to product quality resulting from such manufacturing methods and the measurement itself can vary widely depending upon the approach used. Furthermore, the measure of a co-printed part may not be representative of actual printed components. This project will involve correlating measured density to product performance (strength, toughness, etc.). The students will focus on co-printed tensile or Charpy V-notch samples as a test case and compare the sensitivity and repeatability of different density measurements, assess the appropriate benchmark density, compare co-printed and actual component density, connect density measurement to measure of product performance, and finally comment on whether differences from theoretical density may be related to composition changes (oxygen uptake for example) rather than the presence of porosity.
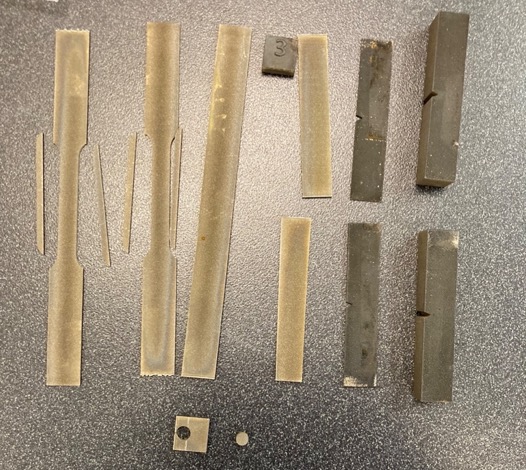
Project 5
Additive manufacturing of a non-metallic valve seat
Duration:Two semesters
Team Members:Haley Jones (lead),TafimulTasif, Brett Paulson, Gavin Van Skiver, Juanita Pombo, LaurenDefesche
Synopsis:Additive manufacturing is an innovative method for manufacturing materials that is gaining traction in various industries. Specifically, we are exploring ways to exploit additive manufacturing to print spare parts at or near site. Typical hydrocarbon production systems and components require the use of non-metallic seal packings,o’rings, and/or seats as primary or secondary forms of containment to aid in production assurance. Such sealing components can be made of thermoplastic or elastomeric materials, i.e.Aflas, Nitrile Rubber (Buna-N/NBR), Hydrogenated Nitrile Butadiene Rubber (HNBR),Perfluoroelastomer(FFKM), Viton (FKM), Teflon (PTFE), Polyether Ether Ketone (PEEK), etc. These materials may be exposed to production chemicals and/or production fluids and are relied on for hydrocarbons flow assurance. Some of these involve high temperatures which can be challenging for seals to perform adequately as their physical-chemical-mechanical properties are impacted by the fluids they are in contact with. In this project, students will design, produce, test, and characterize additive manufactured non-metallic samples based on ASTM standards out of nylon 6/66. The main objective is to provide enough support to whether additive manufacturing is a suitable technology for the manufacturing of the valve seats.
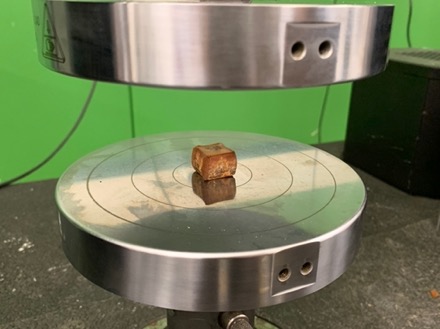
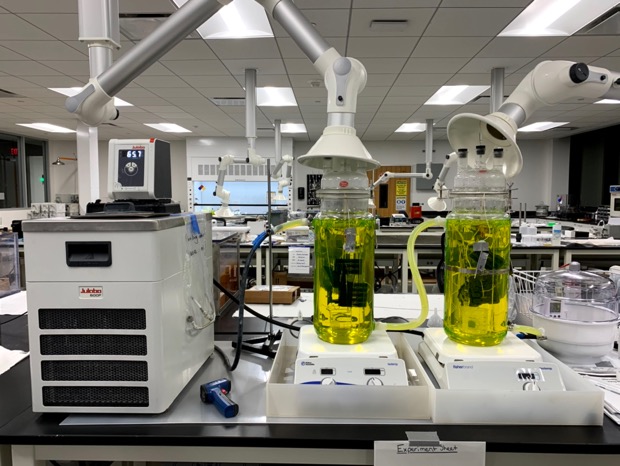
Project 6
Material chemical compatibility analysis
Duration:Two semesters
Team members:Nathan Anderson (lead), Christina Abraham, Austin Parmer,JarianGalloway, Noah Sharp
Synopsis:Typical subsea chemical injection systems require the use of elastomeric seals as primary or secondary forms of containment to aid in production fluids flow assurance. Such seals can be made of elastomeric material, i.e.Aflas, Nitrile Rubber (Buna-N/NBR), Hydrogenated Nitrile Butadiene Rubber (HNBR),Perfloroelastomer(FFKM), Viton (FKM), Teflon (PTFE), etc. These elastomers may be exposed to production chemicals and production fluids at certain production conditions. Some of these involve high temperatures which can be challenging for seals to perform adequately as their physical-chemical-mechanical properties are impacted by the fluids they are in contact with. This is significant to industry as it will be included in the existing material – chemical compatibility testing often referred to by projects or operations for materials selection. In this project, the students will design a test cell, characterize seal material properties when tested in accordance with industry standards for compatibility with other chemicals, and perform material chemical compatibility tests of selected elastomeric seal at three different temperatures when exposed to a selected chemical and evaluate impact on seal’s service life.
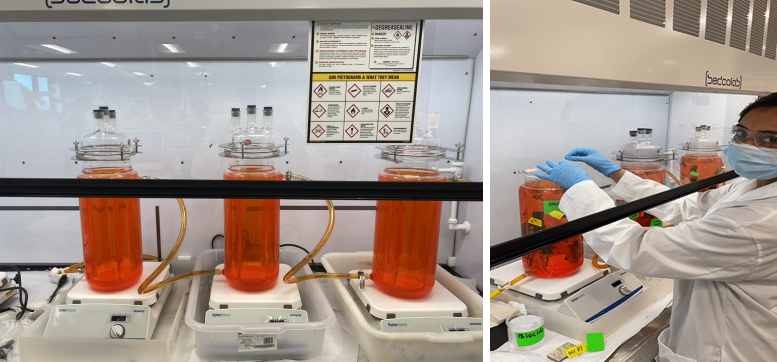
Project 7
Thermodynamic modeling of compression molded thermoplastics
Duration:Two semesters
Team Members:Addison Beard (lead), Benjamin Bui, Elyse Harman, Evie Hart, Tori Page
Synopsis:Transformation of high-temperature thermoplastics in powder form into large cross-section consolidated stock shapes by compression molding is a common industrial molding technique. The primary challenge in this molding technology relates to the thermal properties of the mold system and the polymer material inside the mold, as the control of or accurate indication of these thermal properties relate directly to the quality of the article being molded. Given that this molding technique does not allow for extensive instrumentation, and that the cross-sections are large compared to other melt molding processes, it is required that modeling be used to provide indications of the thermal gradient, heat transfer and viscosity profile during heating and cooling stages. This modeling effort will contribute to consistency in product qualities and reduction in material cost through defect reduction.
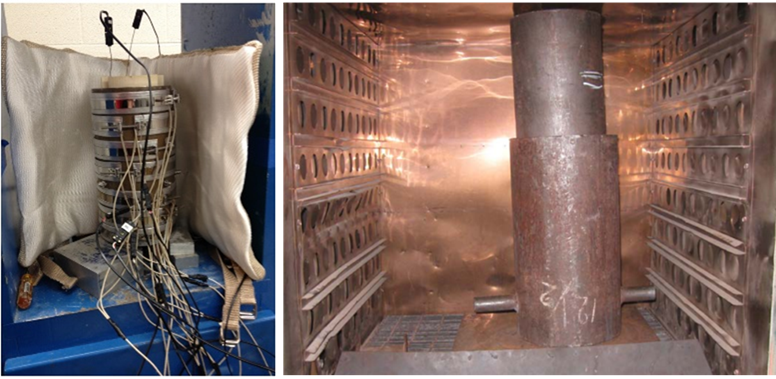
Project 8
Non-Beam Additive Manufacturing of Metals
Duration:Two semesters
Team members:RisheilOrtiz Ayala (Lead), Devyn White, Gregory Wong,KazzandraAlaniz, ZacharyTheimer
Synopsis:We are interested in investigating the capabilities of non-beam metal AM technologies (e.g. material extrusion AM and binder jetting) to improve expedient manufacturing for both military and civilian applications. In this work, students will analyze the correlations between process parameters and mechanical properties of structural metal components produced by these technologies. In this project, students will produce metal structural components via non-beam metal AM, characterize the resulting microstructures and mechanical properties, and relate these properties to the AM processing and sintering parameters. The goal of this project will be a report on the correlation between processing parameters and resulting properties of structural metal components produced by these emerging manufacturing technologies. The Sponsor has a long history of powder metal processing and resources and equipment for both non-beam metal AM printing and thermal processing (i.e. sintering). Therefore, the sponsor will provide resources for printing and sintering samples, as well as expertise and recommendations for powder handling, sintering thermal profiles and atmospheres, and characterization procedures.
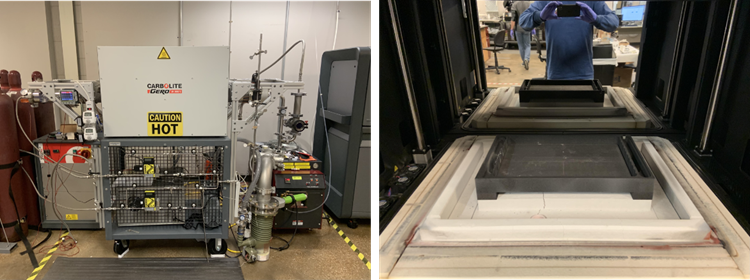
Project 9
Design and cast a functioning Thor’s Hammer
Duration:Two semesters
Team members:GrantHelmich(Lead), Aaron Kucera,AbdallahameenBello, Andrew Balog, Austin Whitt
Synopsis:这个项目的一部分,每年的竞争热点nsored by the Steel Founders’ Society Foundation. The project is focused on the use of modern computational tools to design and produce a functioning Thor’s Hammer. The hammer should not be longer than 20 inches, should not weigh more than 6 pounds and should resemble the Thor’s hammer. The final Hammer will be put to a series of performance tests by a panel to prove worthiness of the implement, similar in style to those seen in the History Channel program, Forged in Fire. The participation in the competition also requires a project video and technical report documenting the design and manufacturing process. In addition, the hammer casting should utilize the casting process to the fullest extent possible to get the best quality, unique features and near net shape.
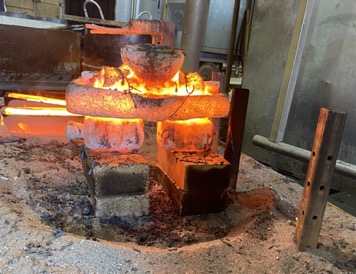
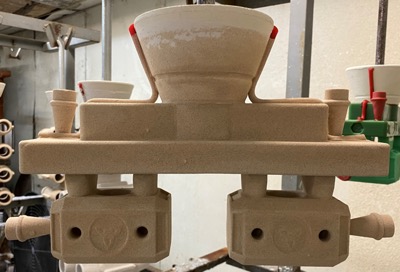
Contact
For information about fall 2020-spring 2021 capstone projects, please contact:
Homero Castaneda
教授,材料科学和Engineering
Email:hcastaneda@tamu.edu